Time is money. No one likes to wait, it’s just the fact of life. Waiting in queues, for delivery, calling customer service to find out the status of your order – we’ve all been there and we surely didn’t find it an enjoyable experience.
This is exactly why manufacturers, suppliers, and all other types of businesses, in general, should get their products out as fast as they can. These are the keywords to make your business better: take time, lead time and cycle time. By measuring and tracking the figures of those critical times you’ll make your business much more efficient and your customers happier.
In this piece, we’ll look at the definitions, calculation formulas, and strategies you can employ to implement takt, lead, and cycle times in your business.
By the end of this guide, you’ll learn
- Meaning of takt, lead, and cycle times;
- Formulas of takt, lead, and cycle times;
- Examples of takt, lead, and cycle times;
- Effective reduction strategies of takt, lead, and cycle times.
Takt time
Takt time definition
Takt time is the average time between the production of two units, which is needed to meet customer demand; in other words, it’s the rate of production required to match the demand.
Suppose your customer wants 20 produced units, then given a 40-hour workweek, the average time to produce one unit should be no more than two hours, and even less than that, provided time for downtime, employee breaks, and other variables. If for some reason, it takes more than two hours to produce a piece in the above example, it means that some corrections are needed by adding the resources, optimizing the production process, or leveling the demand.
According to Wikipedia, the term takt time is borrowed from the Japanese word takuto taimu, which, in turn, was borrowed from the German Taktzeit, meaning “cycle time.”
Takt time formula & takt time calculator | how to calculate takt time
To determine takt time, use the following takt time equation:
T = Ta / D, where
T is the takt time or time between two consecutive units;
Ta is the net time available for work per period;
D is the demand or units that are required to produce per period.
In the above formula, net available time must exclude any variables such as scheduled maintenance, team briefings, and employees’ break times, among other allowances for stoppage times.
There are multiple online services and tools available to calculate takt time. Such as Takt Time Calculator from Zoho, among others.
Let’s look at a takt time example.
Suppose you have employees working a shift per day for nine hours with a lunch break of one hour and 30-minute break per day. Accounting for an average downtime of 20 minutes per day, you end up having 430 minutes of available time per shift. Now, customer demand is 100 pieces a day. The takt time is therefore 4.3 minutes/piece.
Why is takt time important?
Takt time, which is frequently used within lean production lines, has become an essential measurement in ensuring that each production item flows through each build station in the most efficient manner.
Lean manufacturing, in turn, is an approach based on the goal of diminishing waste. By implementing takt time, the waste diminishes because the company processes align with the actual demand.
Takt time also serves the purpose of optimizing and balancing the work content within each build stage, so if for any reason operators finish a stage quicker or struggle to keep pace, the engineering teams will look at ways of rebalancing production.
Another benefit of takt time implementation is increased visibility for production line supervisors and operatives. While calculating and measuring takt time, each build stage is broken down for further observation and analysis, which allows supervisors to react quickly to any changes in timing or production output.
How to implement takt time
Although takt time has an easy calculation formula, it’s not that easy to implement and, just as with any process, it’s best to be rolled out incrementally.
What follows is an example suggestion on how to implement takt time.
First, start off with measuring individual cycle times (more on cycle times and their calculation later in this guide), then insert the calculated data in the takt time formula to come up with the takt time figure.
Divide the work that goes into the process into value-adding and non-value-adding activities.
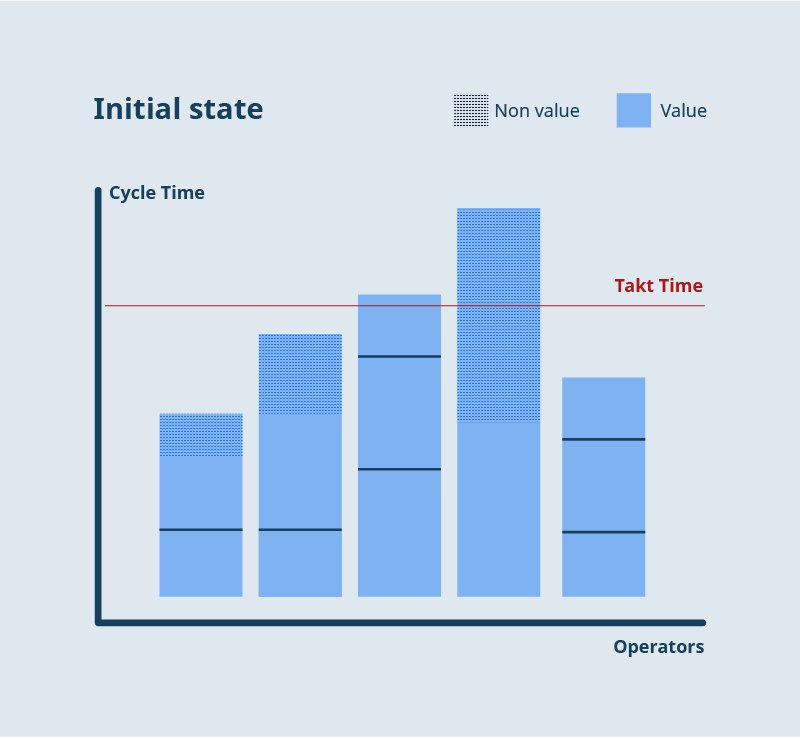
Eliminate activities that do not add value and balance out the value-adding activities equally among the operators.
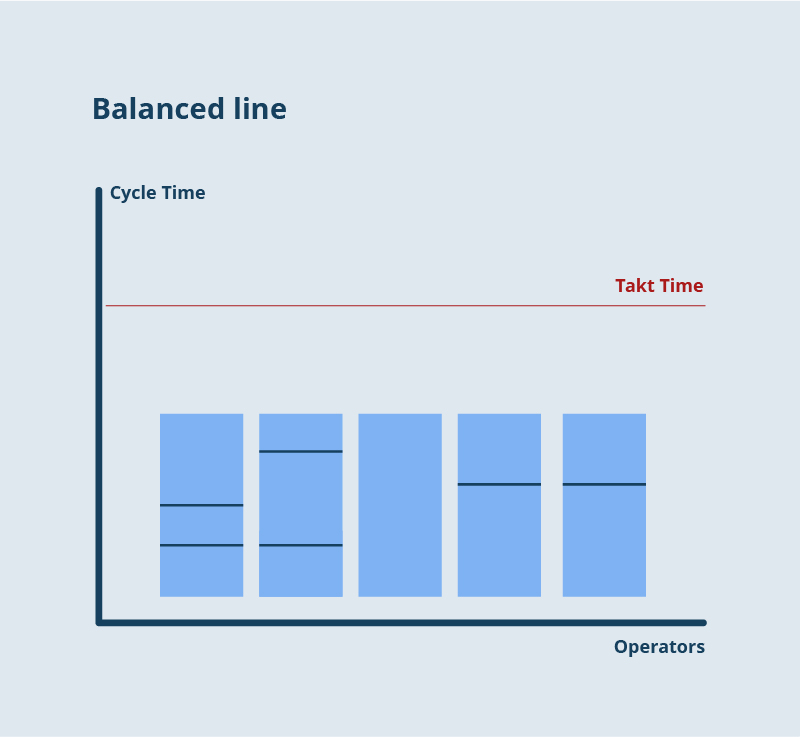
Bring cycle time to takt time and keep the line balanced.
Some manufacturing processes require much more processing time than the takt time — in this case, to achieve needed takt time, more operators should be added to the process. To understand how many operators are needed for a particular operation or build stage, perform the following calculation:
Number of Operators = Total Work Time / Takt Time
For example, suppose, your takt time is two minutes, and it takes 8 minutes to produce a certain piece, then you’ll need four (8/2 = 4) operators to produce it.
Lead time
Lead time definition
Lead time meaning is a latency (delay time) between the initiation and completion of a process.
According to Wikipedia, manufacturing lead time is often defined as the total time required to manufacture an item, including preparation time, queue time, setup time, run time, move time, inspection time, and put-away time.
So what does lead time mean? To put it more succinctly, a lead time is the amount of time that passes from the start to the conclusion of the process.
Lead time measurements get reviewed in pre-processing, processing, and post-processing stages to optimize the (production) process and ultimately to minimize the lead time as much as possible. By comparing lead time throughout the production/post-production processes, managers establish benchmarks against which they can compare the numbers and determine when and where inefficiencies exist.
Different types of lead time
Let’s look at several examples of lead time to better understand the differences between the definitions of lead time in various industries and across different business processes.
- Customer lead time is the time between order confirmation and order fulfillment (which can be either delivery or pickup);
- Material lead time is the time between order placement with a supplier and order receipt;
- Factory (or production) lead time is the amount of time it takes to produce and ship and item provided the materials are available;
- Cumulative lead time is the material time plus factory lead time or the total time it takes from the confirmed order to delivery if you don’t have any materials on hand and have to order.
Lead time calculator & formula
Determining lead time is important for scheduling and manufacturing processes, which all experience a time lag between the start of the production process or order to its completion or receipt. To account for that time lag, you’ll also need to estimate the extra time and allow for it in your planning.
Lead time calculation will differ from business to business, from department to department, or from process to process and will include different variables (or times) for calculation.
For example, to calculate lead time in inventory management, you’ll need to determine the supply and reordering delays and sum them up, like so
Supply delay in days: 2
Reordering delay in days: 1
Lead time: 3
In the above formula, supply delay is the time for the supplier’s shipment to reach your inventory, and the reordering delay is the time for the supplier to accept and process the order. If your supplier accepts orders once a week, and you place the order one day before it gets accepted, then your reordering delay equals that of one day.
Why is lead time important?
Lead time is important for many reasons including customer satisfaction, optimization of production and business processes, and so forth. Let’s outline a few of those reasons below:
- Since customers want their purchased goods and services as fast as possible, calculation and minimization of lead times are important for overall customer satisfaction;
- Manufacturing lead time has a direct relationship with the amount of inventory that exists at different points in the overall supply chain;
- The variation and inconsistency between different types of lead time can result in the stock shortages, which are ultimately preventable provided lead times are carefully managed, calculated, and monitored.
Lead time for small business
Longer lead time impact
Some of the obvious problems that might arise as a result of longer lead times include
- Halts in the production line: If engineers lack components needed for production, it automatically puts a hold on manufacturing operations, which means downtime for business and inability to serve customers on time.
- Inability to generate revenue: The more the deadlines are extended, the greater the impact on business finances. Some businesses that find themselves in this predicament might even order parts from unvetted suppliers and pay more money just to renew the production process and keep up with the customer demands and/or deadlines.
- Contract violations: Because of inability to deliver to customers on time, some businesses may be fined for failing to perform the contractual obligations. Money spent on contract fees could significantly and adversely affect a company’s revenue.
How to shorten lead time
There are a few ways to shorten the delay times:
- Hold the right stocks;
- Integrate suppliers and other businesses vertically, so you don’t depend on external resources and factors that can significantly and unexpectedly alter your estimate lead times — strive to source, manufacture, and assemble internally;
- Reduce cycle times (more on cycle time later), which in turn will shorten the production lead times;
- Have good staffing levels (employee availability) and reliable equipment under preventative (and even autonomous) maintenance;
- Reduce supplier lead time by focusing on sourcing local and more reliable suppliers, establishing long-term contracts, and improving business relationships;
- Establish stocking agreements and agree on vendor stock holds;
- Change shipping methods to more frequent or faster ones;
- Have accurate budgeting, forecasting, and planning procedures in place;
- Reduce low runners and product or component variations.
Examples of lead time implementation
For production and manufacturing
Calculating and implementing lead time in manufacturing is imperative for many reasons: it helps to better a company’s internal processes, improve production efficiency, enhance customer satisfaction, and increase product sales. The increase in sales ultimately improves the company’s financial performance and increases access to capital.
An effective measure of manufacturing efficiency is lead time, which in manufacturing equals the time period between the placement of an order and the shipment of the completed order to the customer. Manufacturing lead time can also include the time it takes to process and have the part ready for manufacturing once it is received (sometimes referred to as throughput time).
From the above said, lead time involved in the manufacturing process comprises the following:
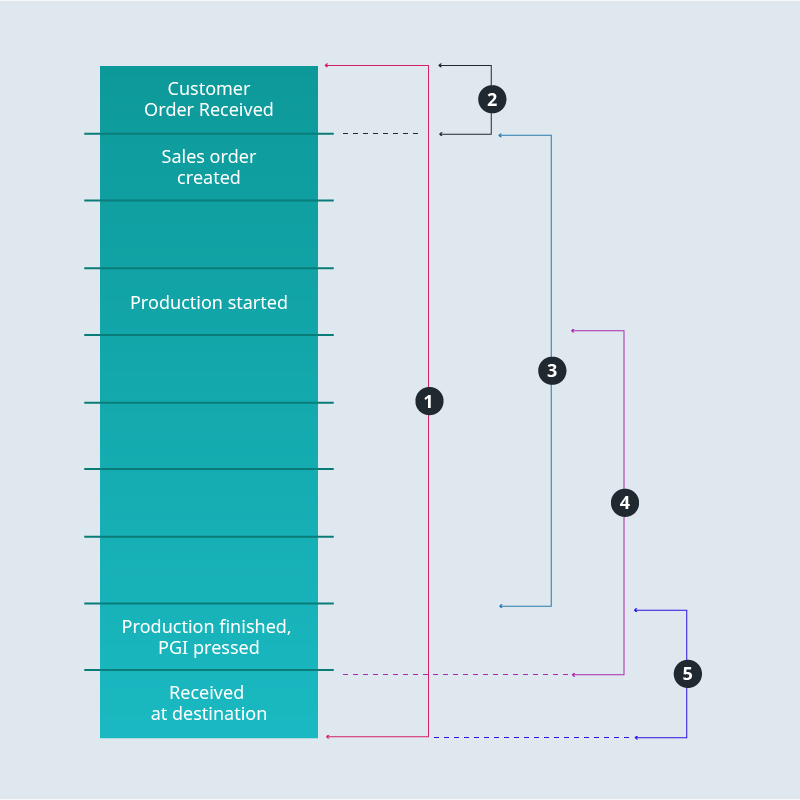
- Order lead time is the time from when a manufacturing company receives a customer’s order to the time the order gets fulfilled. It’s the longest lead time. If the order consists of several deliveries then the measuring ends as soon as the last delivery is fulfilled. The order lead time represents the ability to respond to orders quickly and efficiently.
- Order handling time is the time from the receipt of the order until its acceptance. As soon as the order’s received, the handling time begins and ends when that said order ends up in the system and is accounted for. What’s also important is the order correctness which requires high attention to detail from an operator.
- Manufacturing lead time is the time from the creation of the sales order to its readiness for delivery. Manufacturing lead time is a sort of external measure that is not sufficient on its own: it doesn’t show what and how and how fast an item is made.
- Production lead time is the time from the start of the physical production of the first submodule to the completion of its production. Whereas the manufacturing lead time is an external measure, production lead time is an internal measure: it doesn’t show how fast the product was ready but how long it took to make it.
- Delivery lead time is the time from the completion of production of an order to its delivery to the customer.
There are different types of order lead time, however, and it’s also important to differentiate between those.
Actual order lead time (OLT actual) is the time between the receipt of the customer’s order (aka the order entry date) and the delivery of the goods;
Requested order lead time (OLT requested) is the time between the receipt of the customer’s order and the customer requested delivery date;
Quote order lead time (OLT quote) is the agreed time between the receipt of the customer’s order and the supplier’s committed delivery date of goods (as agreed by the supply chain contract);
Confirmed order lead time (OLT confirmed) is the time between the receipt of the customer’s order and the supplier’s confirmed delivery date of goods.
The differences between those order lead times can be illustrated as follows:
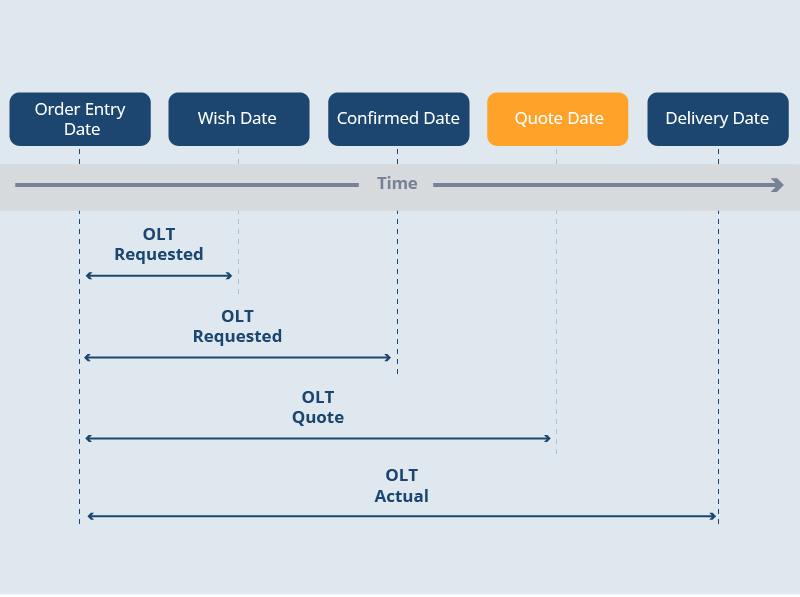
Order lead time formulas:
OLT requested = Wish Date – Order Entry Date, where the ‘wish date’ is the date the customer wants the order;
OLT quote = Quote Date – Order Entry Date, where the ‘quote date’ refers to the date the customer agrees to receive the material;
OLT actual = Delivery Date – Order Entry Date, where the ‘delivery date’ is the day the provider delivers the material;
OLT confirmed = Confirmed Date – Order Entry Date, where the ‘confirmed date’ refers to the date confirmed by the provider to deliver the material in the customer facilities.
Example of manufacturing lead time & lead time in production
A customer makes a phone order for pizza. As soon as an operator accepts that order and punches it in the system, order lead time and order handling time have begun. The order gets sent to the kitchen and is put in the queue. The order gets picked up by the pizza chef who starts preparing it (the production lead time begins). When the pizza is ready, the production lead time stops, and the order is being sent to the delivery guy. The time between the order being picked up by the chef and the delivery guy is the manufacturing time. As soon as the delivery guy picks up the order, delivery lead time begins. When the order gets delivered to the customer, the order lead time stops.
For delivery and shipping
Shipping lead time is the period of time between issuing the instructions to pack the goods to the actual delivery of goods.
Lead times in shipping and delivery are calculated when inventory is prepared and shipped. There are two types of lead times to be accounted for here: internal and external.
Internal lead time is the time it takes to package and prepare goods for shipment. This lead time is used to calculate the earliest possible date that an order can be shipped.
External lead time is the time it takes for goods to leave the warehouse and arrive at the customer’s dock. This lead time is used to calculate the date that customers can expect to receive the goods once they are shipped.
Lead time reduction in delivery
Merchants are always looking for ways to cut down on times it takes to get orders packaged and shipped, especially in such a competitive market with promised one-day or next-day deliveries. Reducing shipping times can certainly give a business an extra competitive advantage. These are a few tips on how to optimize, shorten, or cut down on shipping and delivery lead times.
- Simplify your supply chain: if you get your products from many sources, see how your business can optimize supply vendors. Look for suppliers locally.
- Audit your handling process and see which areas can be tightened up. See if there’s anything that can be automated and processed faster.
- Increase your inventory visibility: detailed knowledge of where your inventory is in the supply chain (from raw materials to finished goods) will help you make more informed decisions and estimations about your shipments.
- Offer to expedite deliveries.
- Ship directly from your vendor bypassing middlemen.
- Outsource your transportation requirements to reliable operators to minimize delivery times.
In supply chain
In supply chain management, a lead time is the amount of time necessary to complete an order cycle (the length of time between the receipt of an order from a customer to the receipt of the order by the customer). Each element of the order cycle is a subcycle with its own lead-time.
In the absence of finished or work-in-progress goods, a lead time is the time it takes to manufacture the order without any inventory other than raw materials.
Total lead time is a combination of internal and external lead times. In supply chain management, an internal lead time is a time it takes for the buying organization’s internal processes to progress from the identification of a need to the issue of a purchase order. External lead time is the time required for the supplying organization’s processes, such as manufacturing, dispatch, and delivery.
These are a few suggestions on how to optimize supply chain lead times:
- Automate inventory management processes: relying less on manual data entry speeds up inventory management, reduces errors, and cuts labor costs;
- Analyze intralogistics processes and sub-processes in detail: detect bottlenecks that delay the flow of materials;
- Provide accurate sales forecasts to suppliers: give your suppliers estimations of your demand, so that they know in advance what to expect from you in the nearest future;
- Increase the frequency of orders: instead of creating bulk orders, which create longer lead times, create smaller and more frequent orders;
- Use local suppliers and reach collaborative agreements whenever possible.
In inventory
Lead time in inventory management is the time between the placement of an order to replenish inventory to the time it’s received, which affects the amount of stock a company needs to hold on to at any point in time.
As have been mentioned above, lead time in inventory is the sum of the supply delay with the reordering delays in days. The longer the lead time, the more stock is needed to hold in inventory, because longer lead times make deliveries unpredictable and force companies to rely on demand forecasts in order to accurately anticipate how much inventory should be stocked at any time.
These are a few tips and factors you can consider to shorten lead times in inventory:
- Increase the number of orders but decrease their volume: order small amounts that take less time to produce and ship rather than make bulk orders that take a lot of time to manufacture. This way your inventory is replenished frequently and on a regular basis: you won’t have to worry about having something out of stock.
- Issue bonuses to suppliers and introduce other perks: if your suppliers deliver well in advance or have been consistent with their deliveries long-term, it makes sense to incentivize their work and issue bonuses (or fines and penalties if the opposite happens) and motivate them to deliver on time.
- Automate your inventory management: by using automation tools you can speed your time to market as less time will be spent on tracking stock levels and creating purchase orders.
- Support local suppliers: go local whenever possible (shipping from other cities and from overseas will obviously make your lead times longer).
For ordering
As already mentioned above, the order lead time is a time period between placing an order and receiving an ordered item. An order handling time is the time from customer order received to customer order created. Both parameters are crucial for understanding a company’s order management prowess.
There are several types of order lead times, which we’ve also mentioned earlier, such as the actual order lead time, the requested order lead time, the quote order lead time, and the confirmed order lead time (the calculations for each type have also been given above in the section on Examples of Lead Time implementation: For production and manufacturing).
Calculating order lead times is important for at least a few reasons:
- Improved understanding of consumer behavior in the market;
- Detection of errors and flaws that hamper the terms of agreement and timely rectification of those errors;
- Improved relationship with consumers;
- Increased profits that are in line with order demands;
- Fewer returns;
- Fewer Service Level Agreement breaches.
In procurement
Lead time in procurement refers to the total time it takes to deliver a product to the end consumer through all stages of production from the moment the product’s ordered. This data allows for better planning of all material procurement procedures and ensuring smooth operation flow.
Let’s consider an example. Imagine a company decides to keep an inventory at a high level thinking it will decrease lead time and make for faster deliveries. While customers can, in fact, benefit from faster deliveries and appreciate the tactics, it’s quite a risky maneuver and requires a change of strategy. Crowded stock can create a product queue and increase (rather than decrease) crossover time and warehouse overheads. Purchasing well in advance is harmful for many reasons: materials can arrive earlier than expected and, in case they are easily perishable or toxic, they can even become dangerous. Moreover, the accumulation of inputs can disrupt other processes.
In order to effectively manage the stock and decrease procurement lead times, businesses need to implement a series of crucial steps and procedures, such as carefully planned procurement management, supplier management, and supply chain management. Having an electronic procurement system in place is of great help since it tends to automate tedious tasks that are prone to human error or labor-intensive and time-consuming.
Tesla lead time example: 40 steps in 90 minutes
A perfect example of the superior management of lead times is often exhibited by car manufacturers. Take Tesla, for example. On Wednesday morning, July 1, 2020, Elon Musk congratulated Tesla employees for hitting their production and delivery goals despite the pandemic. And although Tesla plants had to close for a few weeks due to COVID-19, Tesla returned to full operations by obtaining a full clearance from the government to do so.
How come the car automaker hit its targets even with a temporary shutdown of factories?
According to InsideEVs, a magazine dedicated to electric vehicle news and analysis, part of Tesla’s success can be attributed to engineering efficiencies: imagine that it takes only 40 steps and 90 minutes to produce a Tesla Model 3.
According to Pierre Ferragu, an analyst from New Street Research, who visited the factory Fremont and observed the assemblage, Tesla’s simplicity was unbelievable:
“We could see the Model 3 assembled, from an empty body to a fully functional car in a bit more than 40 steps and 90 minutes, on a line about 1,000 feet long.”
Pierre Firragu
Compare that to an average traditional manufacturer, who could take up to 200 steps till the final product. 40 steps and 90 minutes amounts to 7,000 units per week, which makes it roughly 2 models per second (1.7 to be exact, provided for standard 40-hour 5-day workweek).
The efficiency of such a speedy production and deliveries can be attested to a well-documented process, adherence to lean manufacturing principles, simplified auto lines, robotics that increases speed and accuracy of production, dedication to doing as much work internally as possible (without unnecessary outsourcing), and automation of labor-intensive processes.
Cycle time
Cycle time definition
Cycle time is the time a team spends working on producing an item, or the time it takes to complete one task, which includes both the production and wait times between active work stages.
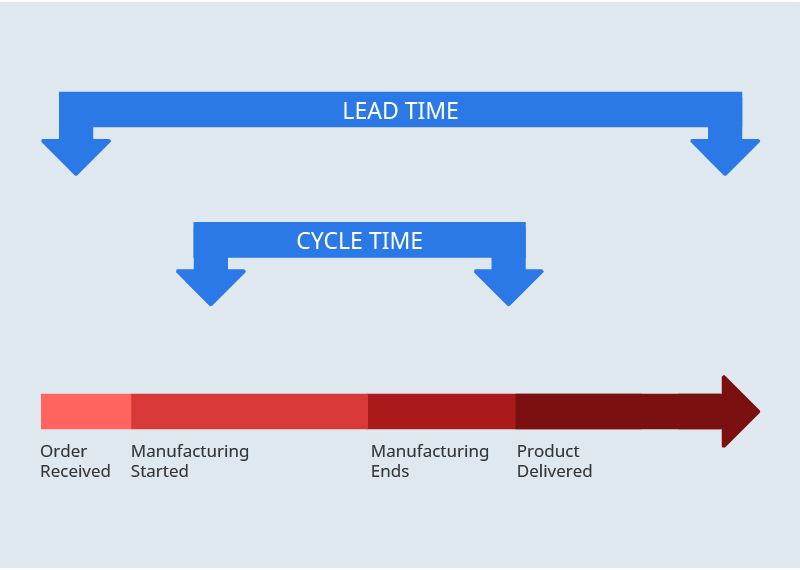
Cycle time formula & cycle time calculator
Now, let’s figure out how to measure cycle time. To calculate it, you’ll need to know two variables: the total number of goods produced and the total time it took to produce those goods. In other words, the cycle time formula looks as follows:
Cycle time of a process = net production time/number of units produced.
Suppose, your team produces 40 units during the 40-hour workweek, then your team’s cycle time will be 1 hour.
Let’s also define different types of cycle times:
- Customer Order Promised Cycle Time is the expected time from a customer order being placed to the time of its delivery.
- Customer Order Actual Cycle Time is the average time taken between a customer placing an order until the delivery of that order and includes the time taken to complete all stages in the fulfillment process (credit checks, picking up the order in the warehouse, shipping time).
- Manufacturing Cycle Time is the time required to convert raw materials into finished goods (i.e. manufacturing cycle time equals the sum of process time, move time, inspection time, and queue time).
- Purchase Order Cycle Time is the time between the receipt of the purchase order to the purchase order’s transmission to the vendor or supplier (i.e. purchase order includes all activities associated with that order such as data input, time taken to confirm receipt by the supplier, time taken to respond with confirmation of pricing and delivery).
- Cash to Cash Cycle Time is the time between paying for raw materials and getting paid for the finished product.
Cycle time examples
Cycle time in supply chain
Supply Chain Cycle Time is the sum of the longest lead times for each stage in the cycle (i.e the total time taken to fulfill a customer’s order if all inventory levels in a supply chain are at zero).
Supply chain cycle time demonstrates the effectiveness and the overall efficiency of the supply chain: short cycles make for an agile supply chain, whereas the longer cycles indicate inherent problems with the supply chain management.
The mapping of the supply chain management process can help identify the cycle times that should be adjusted. For example, if the delivery cycle time is 70 days but only 20 days are actually spent adding value to the product, then it needs to be optimized so that delivery time is reduced and corresponds as closely as possible to the time spent on adding value. The business might hire a consultancy or create a special task force within the organization to cut back on non-value-added activities.
Cycle time in production
Manufacturing cycle time (or production cycle time) also known as throughput time is the time it takes to convert raw materials into a finished product.
Production cycle time = Process time + Move time + Inspection time + Queue time
For example, the ABC company has calculated the time it takes to complete various activities as follows:
Wait time 3 days
Process time 8 days
Inspection time 3 days
Queue time 2 days
Move time 2 day
The manufacturing or production time is therefore 15 days. The delivery cycle time, though, must include the wait time, hence, it’s 18 days, meaning that on average the company spends 18 days from the receipt of a customer order to the delivery of the product.
Effective ways of cycle time reduction
Before you even start cutting back on cycle times, you should have a solid plan or a process map that includes such variables as inputs, outputs, distances, organizations involved, suppliers, vendors, responsibilities, value-added and non-value-added times and activities.
Then define your customers’ expectations, which is imperative for establishing the ongoing supply-demand relationship. Each of your customers, if possible, should have their own profile with at least five parameters, such as volume, variety, velocity, visibility, and variation:
- Volume indicator means how many products your customer wants and needs;
- Variety means the size, type, model, color, or a particular configuration the customer asks for;
- Visibility is the time between the customer expressing their needs and actually showing up for the product, placing an order, or paying for it;
- Velocity means the resources required to deliver the product once the customer requests it;
- Variation is the change in the size of the customer’s order and how it affects the current processes.
As soon as you define your customer demand profiles, you should match them against supply profiles. Long cycle times happen when a process doesn’t have sufficient capacity to fulfill your customer’s demand. The identification of a processing capacity involves matching a customer demand profile with a process supply profile on a task by task basis and figuring out the tasks where the two are significantly out of sync.
Some of the major causes of long and extended cycle time measurements include
- Logistics;
- Overproduction;
- Bureaucracy (such as unnecessary reviews and approvals);
- Defective products and rework of defective products;
- Work accomplished on activities customers didn’t ask for.
After identifying bottlenecks, proceed to implement the following strategies that will help reduce the cycle times substantially:
- Eliminate or reduce non-value-added activities;
- Realign the organization and remove unnecessary paperwork that can contribute to longer cycle times;
- Automate tedious and laborious processes;
- Implement any system that increases productivity and speed up task-delivery by ensuring your team takes up on work that they have the capacity to do;
- Attack cycle time losses at the source — expose problems as soon as they occur (employ scoreboards and interval controls to find out information in real-time and encourage operators to take immediate action);
- Monitor your cycle time continuously and perform simple time studies for each process you run.
Takt Time, Lead Time, or Cycle Time
To sum it all up, let’s briefly outline the differences between those three terms in the table that follows:
COMPARISON POINTS | TAKT TIME | LEAD TIME | CYCLE TIME |
---|---|---|---|
Definition | takt time (or takt time) is the maximum acceptable time to meet the demands of the consumer (or the rate of work to meet customer demand). | Lead time is the time between the initiation of an order and its completion (or the delay between the start and end of a process). | Cycle time is the time between the beginning and ending of the process (or the time it takes to finish one product). |
Formula | Takt time = Net available time for production/Customer’s daily demand | Lead time = Task 1 — Task 2 | Cycle time = Net production time/Number of units produced |
Objective | -Avoid under or overproduction-Maintain constant production flow-Set realistic time targets and diminish waste-Increase efficiency, decrease training times, and minimize overtime | -Improve the production rate-Improve the additional processing rates (production logistics and shipment)-Enhance customer satisfaction-Increase product sales | -Make adjustments to the production time to meet customer demand-Provide meaningful data to adjust the lead time |
As a side note, it’s worth noting that since at the bottom of every business KPI (especially those mentioned above, be it takt, cycle, lead times) lies time, it’s important to keep track of it and separate net production time from your downtime. Lamanche is an effective, user-friendly, simple yet robust time tracking software that can help you track times spent on tasks, projects, as well as employee’s overall time spent on the job.
If you have found a spelling error, please, notify us by selecting that text and pressing Ctrl+Enter.
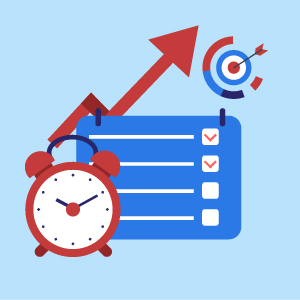
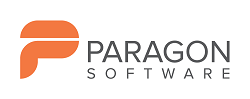
Leave a Comment